A New Life for Waste Plastics and Coffee Grounds
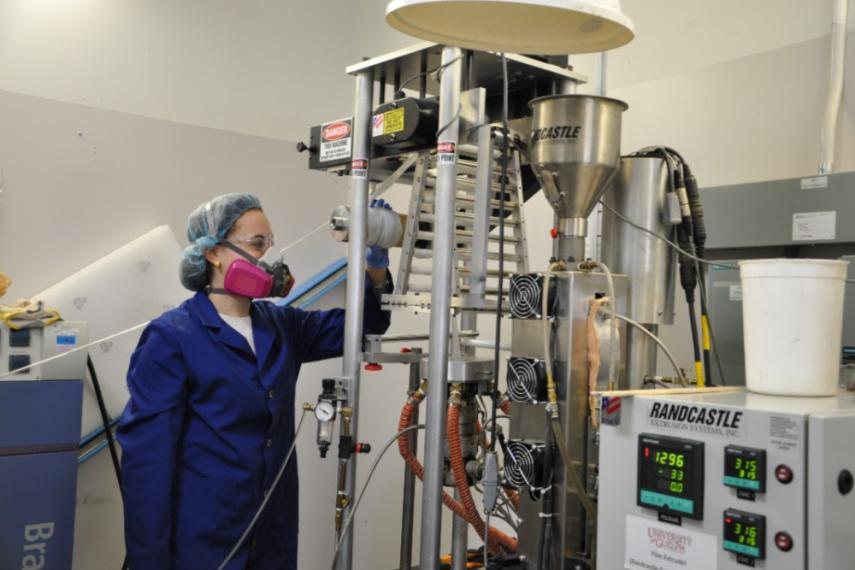
Water bottles and spent coffee grounds used to develop 3D printing materials and rigid packaging.
Today, about 400 million tonnes of plastic is produced annually, with roughly 80 per cent entering landfills or leaking into the natural environment. The primary contributor: single use plastics. Polyethylene terephthalate (PET) is a heavily relied upon single-use plastic that is found in everyday products such as water bottles, electronics and household items. Similarly, the large quantity of plastic bale wrap that farmers use to store straw and hay is made from linear low-density polyethylene (LLDPE) and is often sent to landfills after use. Researchers have been investigating ways to turn plastics like PET and LLDPE into new value-added products, such as biocomposites.
A biocomposite is a composite material (which combines two or more base materials with distinct properties) containing plastic resins and/or fillers obtained from natural resources. Biocarbon is emerging as a filler and reinforcing agent in biocomposites. Biocarbon can be created by heating organic matter, including used coffee grounds, to a high temperature in a low oxygen environment – a process called pyrolysis. In Canada, an estimated 300,000 metric tonnes of coffee are consumed annually. Thus, many researchers are attempting to find new uses for waste coffee grounds generated in the coffee brewing process.
Coffee grounds used to develop biocomposites a step towards environmental sustainability.
Dr. Manjusri Misra, a professor in the School of Engineering (SOE) at the University of Guelph (U of G), and Dr. Amar Mohanty, an Ontario Agricultural College professor in the Department of Plant Agriculture (cross-appointed to SOE), set out to produce biocarbon from used coffee grounds. They then tried to use this biocarbon, along with a blend of recycled PET and LLDPE, to develop sustainable biocomposites. The team collected spent coffee grounds from the U of G campus and used pyrolysis to convert them to biocarbon.
Next, the team made plastic pellets from water bottles from a grocery store. They mixed the pellets as well as bale wrap they collected from a local farmer at a ratio of 80 to 20 to fabricate a plastic blend. Four different biocomposites were created by mixing the fabricated blend with five, 10, 15 or 20 per cent of biocarbon. These biocomposites were then evaluated for their strength, morphology, dimensional stability, and thermal behavior in the temperature range between -50 degrees Celsius and 850 degrees Celsius.
They found that the incorporation of five per cent biocarbon obtained at 500 degrees Celsius and 10 per cent biocarbon at 900 degrees Celsius produced a biocomposite that demonstrated balanced strength, stiffness, and flexibility properties and suitable melt flow behavior – most promising for rigid packaging and 3D printing applications.
“We successfully created biocomposites composed of 95 per cent sustainable input materials, displacing the fossil-based resources,” says Misra. “Furthermore, our biocomposites are potential candidates for industrial uses such as packaging and additive manufacturing. This new research to utilize recycled waste materials to produce biocomposites would be a significant step towards reducing our environmental footprint and achieving the global sustainable development goals.”
Dr. Manjusri Misra is a Professor and a Tier 1 Canada Research Chair in Sustainable Biocomposites in the School of Engineering with a joint appointment in the Department of Plant Agriculture.
Dr. Amar Mohanty is a Professor in the Department of Plant Agriculture and Ontario Agricultural College Distinguished Research Chair in Sustainable Biomaterials with a joint appointment in the School of Engineering.
Gupta A, Mohanty A, Misra M. Biocarbon from spent coffee ground and their sustainable biocomposites with recycled water bottle and bale wrap: A new life for waste plastics and waste food residues for industrial uses. Compos. – A: Appl. Sci. Manuf. 2022 March. doi: 10.1016/j.compositesa.2021.106759.
This work was supported by the Ontario Ministry of Colleges and Universities – Ontario Research Fund, Research Excellence Program Round 9 grant; the Ontario Agri-Food Innovation Alliance – Bioeconomy for Industrial Uses Research Program grant; and the Natural Sciences and Engineering Research Council of Canada (NSERC) Discovery Grant, Canada Research Chairs program.
For further reference:
Maldonado, B, Pal, A, Mohanty, A, Misra, M. (2021). "Sustainable 3D printed composites from recycled ocean plastics and pyrolyzed soy-hulls: Optimization of printing parameters, performance studies and prototypes development". Composites Part C - Open Access, 100197. doi: 10.1016/j.jcomc.2021.100197